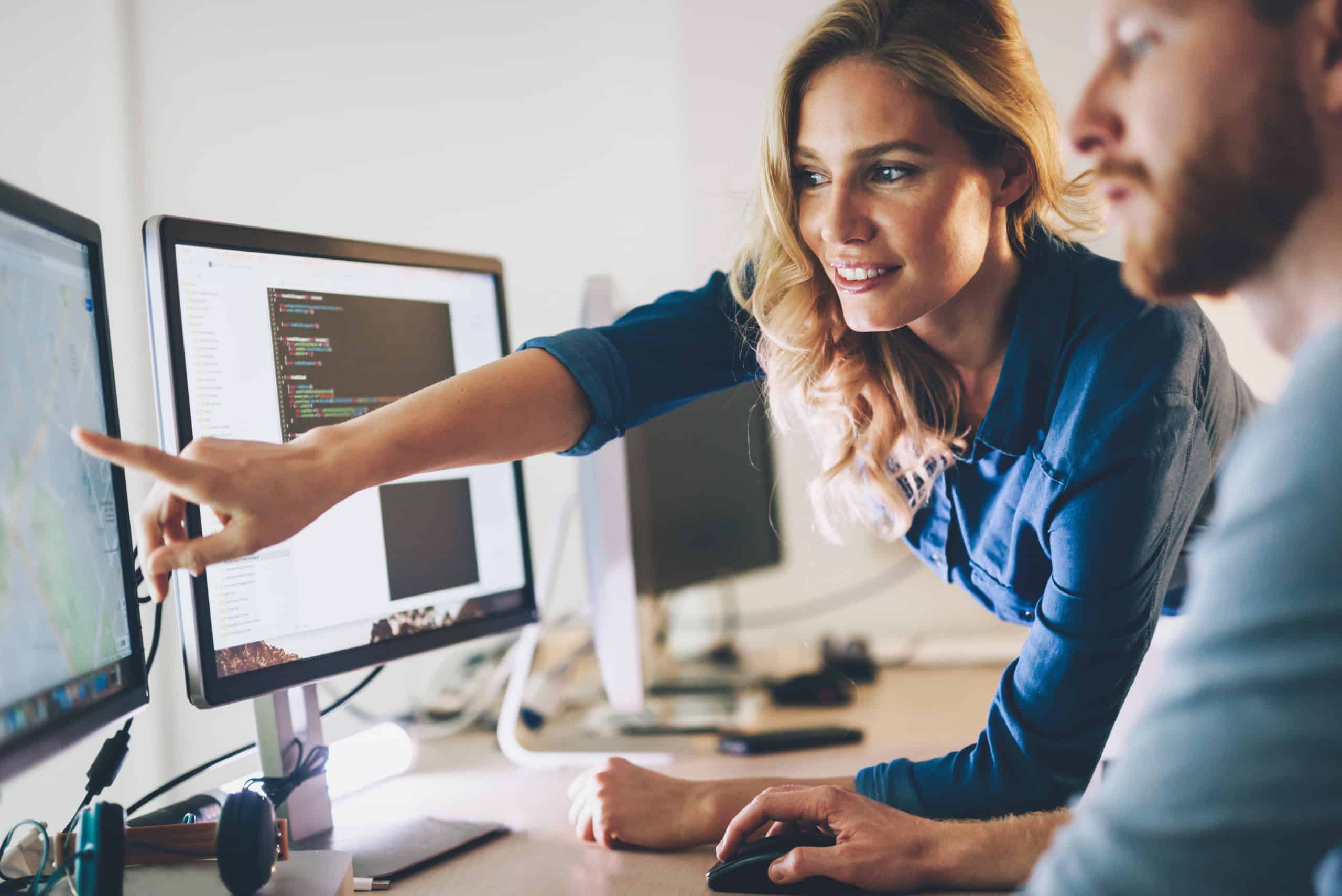
Lean management: a human-being centered philosophy
What do we mean by Lean Management
In the complex, articulate economic scenario within which companies now find themselves nowadays, the ability to react rapidly and effectively to new, unexpected challenges that the world throws up is increasingly important.
As we well know, the lack of resources available for companies, such as money and time, make the search for alternative internal solutions essential to stay competitive with their competitors.
Of the various adoptable solutions, there is Lean management and Agile Methodology. What is it about more specifically?
Specifically, Lean management is defined as a philosophy or rather an approach that involves all company areas across the board.
Starting with the term “Lean”, we already have an idea of what the guidelines of this philosophy will be: a reduction of waste, flexibility, less work in favour or a parallel increase in quality. The need to improve company production process efficacy is behind this approach, to avoid reaching a point of no return where they are forced to halt production.
This phenomenon is called “bottleneck” in technical terms, and is hugely damaging for company competitiveness in terms of wasting resources and inefficiency. In fact, the immediate consequence of this eventuality is a delay in delivering the finished products to end clients.
As first thing, Lean management sets itself the goal of reducing all waste that might occur during the production process, to try to avoid the situation described above from happening. Therefore we can see that, according to Lean literature, there are 7 wastes to avoid:
1. Inventory.
2. Waiting.
3. Defects.
4. Overproduction.
5. Motion.
6. Transportation.
7. Over-processing.
In its application, therefore, Lean Management keeps the creation of value for the end client as a guideline, not measuring said value in terms of price and quantities produced, but in terms of the satisfaction created specifically for each client.
At the basis of this new philosophy, there has to be a radical change in the way of thinking by all those involved, whether directly or indirectly within the company.
Below we will see more in detail how investing resources in worker training is essential from a human point of view, placing them at the centre of the “Lean” changes that are to be addressed.
Why should a company adopt the Lean method?
To be able to answer this question, we must take a look at the advantages that comes from applying this new philosophy in the company. In particular, these benefits are even greater during a historical period such as the current one, where flexibility in company process management underpins the maintenance of market competitiveness.
Advantages:
- Reduction of production and inventory costs
- Reduction of delivery time
- Improvement on quality in spite of quantity
- Lower quantity of workforce needed
- Reduction of wastes in term of resources
Having said that, we can conclude our initial thoughts on Lean management, maintaining how it can bring huge benefits to the company, once the difficulty of making all workers aware of the importance of this change has been overcome.
We will then see how this new philosophy must be internalised by all the company workers, creating a common school of thought that is the foundation of Lean Management, the so-called lean thinking.
The agile method
As we said at the start, Lean thinking is one of the various methods to make the production process competitive and effective. However, there are others.
There is another method, known as Agile, that shares many aspects with Lean thinking. One of these more than the others, the goal of offering a high-quality finished product to the client within the given time-scale.
Let’s try to understand more what it entails; the Agile method refers to a structured approach for project management and product development. It provides the team with a method for being able to respond to change without running into management problems.
In both cases, we can see how these approaches, Lean and Agile, basically aim to:
- Improve production process efficiency via a change of vision within the company, with the goal of improving the quality of the finished product;
- Placing the client and their satisfaction as the main goal.
As we have already emphasised, the Lean Method completely loses its meaning when it is not supported at its foundations by a common school of thought within the company.
There is therefore an extreme need, to be explained to the reader, how the largest investments that the company management must make to obtain a more effective economic return is in staff training.
As part of the Lean method, the change in company processes does not come from the technological improvements, but from a change in philosophy and behaviour by the people who make up the “company” system.
The difficulty that may arise in this phase comes from the fact that there are no predefined patterns to follow. Each company organisation must find its own balance in relation to needs and necessities.
How is it possible to address this change in practical terms?
In this final part of the article, we will see a tool used in Lean management, i.e. The PDCA cycle, that stands for PLAN-DO-CHECK-ACT. This is a method comprising four stages that includes solutions to test, analyse and implement company process management. The end goal to be achieved is to receive client feedback in order to optimise this method whenever it is requested. Now lets look in detail at the 4 stages of the PDCA method:
PLAN: this is the most delicate and important stage: what is the problem that needs solving? Which resources do we need to do that? During this stage, we are addressing the first step in order to then build a correct strategy, without running the risk of future errors.
DO: during this stage, we will apply everything that we have previously analysed. It is important for all members of the team to have a clear idea of the strategy to be adopted, in order to obtain a better result.
CHECK: at this point, it is necessary to verify with the team whether the plan initially drawn up is actually working. Any issues must be identified and eliminated in the future.
ACT: the final stage takes advantage of all the results of the previous stages. If a well-defined plan is achieved, without any weak points, this is the right time to be able to apply it practically.
As a conclusion to our thoughts, we would like to place emphasis on three fundamental aspects, in the hope that the reader can take them away:
– The prime importance of client satisfaction, considered to be the guideline at every step and in every company process;
– The need for companies to manage to be elastic and flexible in internal processes, that can allow them to overcome market challenges;
– The central nature worker human training, starting from the top management and working down to employees, which will make the difference as to whether the lean strategies are successful or not.
Founder of Uppwise, Gioacchino has solid hands-on, experience and vision in the PPM Market, gained as a startupper and founder of a number of software & cloud-services companies. During the last two years he has lead the company transformation, shifting from the offering of a traditional PPM product to a new suite of SPM, APM and CWM products.